Fluidized Bed Reactor Simulation In Aspen Plus
Aspen Plus Fluidized Bed Reactor Simulation:
![]() |
Fluidized Bed Reactor (FBR) |
The fluidized bed reactor is a reactor in which the fluid from the bottom of the reactor keeps the solid catalysts suspended inside the reactor. This reactor has an advantage over traditional packed bed reactor because it has a better heat and mass transfer. In industry, the fluidized bed reactor is most prominently used to produce products which cannot be efficiently manufactured using more commonly using more commonly used reactors (Towler, 2012).
A fluidized bed reactor is used to produce a variety of products. In the fuel industry, a fluidized bed reactor is used to produce gasoline, propane, butane, and propylene (Washington University, 2016). While these are some of the common uses of fluidized bed reactor, good mixing, and energy efficient nature of the reactor allows a fluidized bed to be used in producing a less conventional fluidized bed reactor product such as photovoltaic cells. REC Silicon uses a fluidized bed to produce purified silicon for photovoltaic cells as shown in the picture (Computational Particle Fluid Dynamics, 2016). Unlike the traditional method of covering seed rods with a superheated silicon gas, the method used by REC Silicon lets the seed granules to float inside a fluidized bed reactor. Then, silane gas enters from the bottom and when it comes in contact with the seed granule, the gas breaks down and covers it with silicon. Once enough silicon layer is sufficiently deposited, the larger and heavier granules exit the fluidized bed reactor. This process consumes 80-90% less energy than the traditional method (REC Silicon, 2016).
In order to manually design a fluidized bed reactor which would yield a useful information, myriads of parameters such as porosity at minimum fluidization, minimum fluidization velocity, bubble size, minimum fluidization velocity, velocity of bubble rise, fraction of the total bed occupied by bubbles, fraction of the bed consisting of wakes, volume of the catalyst in the bubbles, clouds and emulsion, mass transfer coefficient between bubble and cloud and additional information must be obtained experimentally (Brown,2008). For most purposes, such manual calculation is not only tedious but also has a great chance of yielding an incorrect result. Instead of carrying out a manual calculation, it is practical to use a simulation software such as Aspen HYSYS. Unfortunately, however, Aspen HYSYS does not have a good way to handle solids in streams. Furthermore, it does not have advanced reactors such as the fluidized bed reactor. Aspen Plus allows the users to handle solids and model a fluidized bed reactor (AspenTech, 2014).
Limitations (Aspen Plus Fluidized Bed Reactor Simulation):
While Aspen Plus allows the simulation to yield as realistic result as possible, the general heuristic is that the catalyst particle sizes should be generally less than a 300 micrometer (Towler, 2012). Also, the fluid of the reactants entering the reactor from the bottom should be above the minimum fluidization velocity of the particle, which is the minimum linear velocity of the reactant to keep the solid particles in the air (Brown, 2008). Furthermore, the simulation may not correctly reflect what really happens in the reactor. For example, Aspen Plus requires an entering and exiting streams of solid particles in the simulation (AspenTech, 2014). However, in a real fluidized bed reactor, a fixed amount of catalyst is put into the reactor and kept from leaving the reactor by controlling the fluidization velocity. The catalysts are switched when their life cycle is done and this switching of catalyst could be modeled as a continuous flow of solid particles. However, it is important to note that what is on the flow sheet of the simulation may not be a correct representation of the real system.
Overall Steps of Aspen Plus Simulation:
Fluidized bed reactor simulations require a lot of equations and parameters. However, the following design equations are the core equations.
In the equations, Kb, Ke, and Kc are the rate constants in bubble, emulsion, and cloud phases respectively. Similarly, Kbc, Kce are mass transfer coefficients between bubble and cloud and cloud and emulsion. Lastly, the three concentrations are the concentration of the species A in three phases. In a fluidized bed simulation, more equations are used to calculate a more detailed result, but these are the most basic and important equations when designing a fluidized bed reactor (University of Michigan, 2016).
In terms of its setup, the fluidized bed reactor simulation in Aspen Plus is similar to those of the other types of reactors in Aspen HYSYS, but different in a sense that information about solid needs to be specified. As the initial step, the units and the components which exist in the system should be set and the property method which is similar to the fluid packages of Aspen HYSYS must be selected to closely model the solids in the actual system. Once all the specification is made, then the input and output streams of the reactants and products must be connected to the bottom and top of the reactor respectively. In addition, the inlet and outlet stream of solid particles must be connected to the left and right sides of the reactor respectively, even though the actual physical system may not have a solid particle stream entering or leaving the reactor. However, if a fluidized bed reactor requires a means of recovering the catalyst solid, a cyclone and a dryer may be used together to achieve to recover the solid particles. Generally, cyclone is a more effective way of separating gas from solid than gravity settling chamber (Peters, 2003). However, fabric filters, venturi scrubbers, and dry electrostatic precipitators are other options for separating solid from gas (Seider, 2004). Also, if there is a need to dry the solid particles, a dryer can be used. Specifically, if the solid particles are sensitive to thermal decomposition, spray drier may be used, as long as the catalyst can withstand the high pressure required for droplet formation (Ulrich 1984). Finally, after all the necessary equipment is set up in the simulator, the mesh and distribution function is checked to see if the reasonable output is obtained from the simulation. In wiki-page, the detailed steps and screenshots obtained from Aspen Tech manual is shown below and the only cyclone is shown in the page for brevity.
Step 1: Solids Flow Sheet Templates:
![]() |
Flow Sheet Templates |
After clicking "New" in the upper left-hand corner, take a note of a variety of installed templates listed in the left sidebar. Select the “Solids” category.
Step 2: Specify Global Units:
![]() |
Global Unit selection |
The desired unit set may be chosen either from the drop down in the Units group on the Home tab, or from the “Setup-> Specifications” of the Navigation Pane.
Step 3: Find Compound:
![]() |
Compound Selection |
Desired compounds must be found and identified as in Aspen HYSYS.
Step 4: Specify Stream as Solid:
![]() |
Solid stream selection |
This is a part that is different from Aspen HYSYS. In some cases, the actual system which we are trying to model only has solid catalysts inside the reactor and if designed properly, the catalysts should not leave the reactor. However, in order for Aspen Plus to model a system with a solid stream, it is necessary to define the solid particles as solid stream.
Step 5: Set Property Method:
![]() |
Property selection |
This step is similar to the fluid package selection in Aspen HYSYS. The only notable part about this step is that for the type of the solid stream, Aspen Plus manual recommends choosing "IDEAL" as this is good enough for most purposes.
Step 6:Specify Property Specification:
![]() |
Property selection |
This step may be required because the properties for solids are different from the conventional properties for fluids.
Step 7: Specify Properties of Desired Compounds:
![]() |
Desired component property selection |
Necessary parameters and components are selected at this step.
Step 8: Specify Stream Class:
![]() |
Stream class selection |
\
Stream class needs to be specified. MIXCIPSD is recommended for conventional solids are present with a particle size distribution.
Step 9: Create PSD mesh:
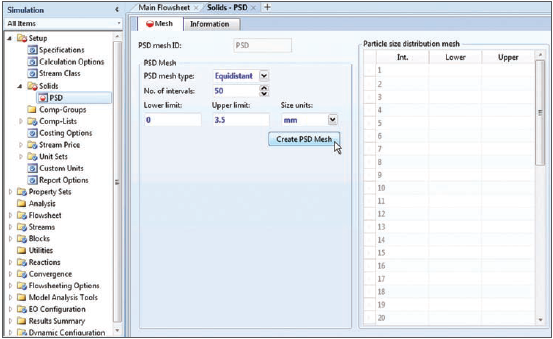
PSD mesh creation
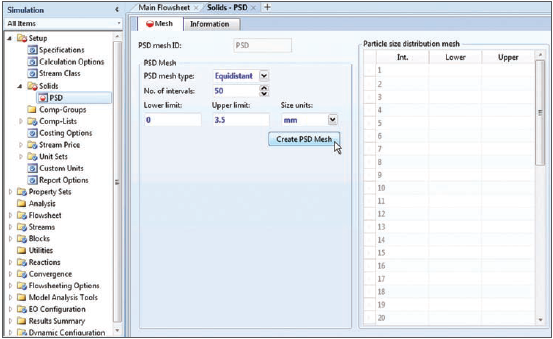
PSD mesh is created and necessary parameters such as the size range of the particle size distribution is set.
Step 10: Create Additional PSD Mesh:
![]() |
Additional PSD mesh creation |
Additional PSD meshes can be created.
Step 11: Specify PSD Section for a CI Solid Form:
![]() |
PSD selection |
If a stream only has a solid component, only fill out the CI Solid tab within this form and leave the Mixed tab blank. If a stream is partially solid, then it is necessary to fill out both streams. Both the Specifications and Particle Size Distribution sections must be filled out at least.
Step 12: Create a New PSD mesh in CI Solid Form:
![]() |
PSD mesh creation in CI solid form |
A previously specified mesh could be used but a new PSD mesh ID can be selected from the drop down menu.
Step 13: Use a Distribution Function:
![]() |
Distribution function used |
This step is done to populate the PSD for a specific stream. After all the inputs are entered, calculate "Calculate" to obtain a plot of the defined PSD. This can be used to check if mesh and function match.
Step 14: Add Reactors and Other Components:
![]() |
Simulation sample |
A fluidized bed reactor is put on the flowsheet. The solid stream enters from the left and exits on the right side of the reactor. In the reaction effluent. The inlet stream of the reactants enters the reactor from the bottom and the reaction effluent exits to the top. stream, some of the solid particles will be included in it. Therefore, a cyclone is used to separate the solids and send it back to the solid stream.
Simulation:
Degrees of Freedom:
A degree of freedom analysis will assist in reaching a state of convergence for the reactor and downstream units (Felder, 2005). For a reactor,
in which the number of degrees of freedom is expressed as the number of unknown variables plus the number of reactions occurring minus the number of material balances able to be performed on the system (Wikibooks, 2014). In order for the simulation to converge, the user must specify as many variables as existing degrees of freedom. The simulation will then calculate unspecified variables
Conclusion:
HYSYS simulations are an excellent starting point for designing a plant; but, they can also be used after completion to check for accuracy in the sizing and rating of the equipment. This will help to ensure that a plant is safe for employees and will have safety precautions in place to prevent dangerous incidents.
As far as fluidized bed reactor simulation is concerned, Aspen Plus is a highly capable tool that allows the user to investigate how different factors affect the design of the actual fluidized bed reactor. Especially after the fluidized bed reactor is simulated, the user can obtain numerous relevant information regarding the reactor such as the dimensions of the reactor and heat removal requirements. However, it is important to note the fact that the output from the simulation needs to be checked constantly to make sure that all of the values fall in a reasonable range. Due to the fact that manual calculation for the fluidized bed reactor is burdensome and requires so many parameters, it is sometimes difficult to check for the reliability of the values given by the simulation. Still, as long as the users are aware of the fact that the simulation may not be perfect, Aspen Plus provides a convenient way to model and handle a process that involves solid and more complex reactors such as fluidized bed reactor.
References:
- "Reactions in HYSYS" Rice University Chemical Engineering Department, [http://www.owlnet.rice.edu/~ceng403/hysys/reactions.html ]"Reactions in HYSYS"
- AspenTech. HYSYS 2005.2 Simulation Basis. Chapter 9 (2005).
- AspenTech. Jump Start: Solids Process Modeling in Aspen Plus. (2014)
- Washington University. Current Applications for Fluidized Bed Reactors. (2016)
- REC Silicon. REC Silicon's Fluidized Bed Reactor (FBR) Process. (2016)
- R.M. Felder, R.W. Rousseau, Elementary Principles of Chemical Processes. 3rd edition, Wiley (2005)
- Wikibooks, Introduction to Chemical Engineering Processes, 2014.
- L.F. Brown, H.S. Fogler, Diffusion and Reaction in Porous Catalysts. Chapter 12 (2008)
- W.D. Seider, J.D. Seader, D.R. Lewin, Process Design Principles: Synthesis, Analysis, and Evaluation, Wiley: New York, 2004
- M.S. Peters, K.D. Timmerhaus, Plant Design and Economics for Chemical Engineers, 5th Ed., McGraw-Hill: New York, 2003.
- G.D. Ulrich, A Guide to Chemical Engineering Process Design and Economics, Wiley: New York, 1984.
Simulations have been used for many years in sectors such as the airline industry and the military. Increasingly, they are being used as an effective learning strategy in many workplaces. There is almost no limit to where simulations can be used. SimFront
ReplyDeleteKissan Agro Industries is recognized as the prominent Seed Dryer Machine Manufacturer and supplier in India. These machines are made available in various specifications. These machines are carefully manufactured with high precision and perfection by making use of high-quality components under the able guidance of our adept professionals. Offered machine is used in the agricultural industry for the seed drying process before it is processed. Besides, our valued clients can purchase this Seed Dryer Machine at a reasonable price. Created obtainable during varied specifications, offered machine is rigorously factory-made with high exactitude and perfection by creating use of top quality parts beneath the in a position steering of our adept professionals.
ReplyDeleteyou may also visit:
dal mill plant manufacturer.
Emery Roll Machine Manufacturer in Delhi,
Batch Type Dryer Manufacturer in UP,
Gravity Separator Machine manufacturer in Delhi,
Patka Machine Manufacturer,
Stone Separator Manufacturer
Our commitment to sleep research, data collection and meticulous testing is evident in every mattress we make.
ReplyDeleteImagine a mattress that responds to your every touch. Our Luxurious Viscoool and Tempagel mattresses adjust to your unique weight and shape, like they were designed just for you.
On our mattresses, you’ll achieve deeper sleep that’s free from aches and pains, and sleep cooler and refreshed thanks to the large, open cells in our memory foam. Find the mattress that’s your perfect fit. Learn why American Beds are the Best Mattresses For You.
Swastik Hydraulic is a leading manufacturer of high-quality shell and tube heat exchangers. We are trusted Shell and Tube Heat Exchanger Manufacturers in New Delhi, known for our precision and performance. Our expertise also extends as reliable Shell and Tube Heat Exchanger Manufacturers in Noida and Shell and Tube Heat Exchanger Manufacturers in Ahmedabad, serving various industries with efficient thermal solutions.
ReplyDeleteWow this is a wonderful blog having all useful information. Reactor Types
ReplyDelete